Product Process
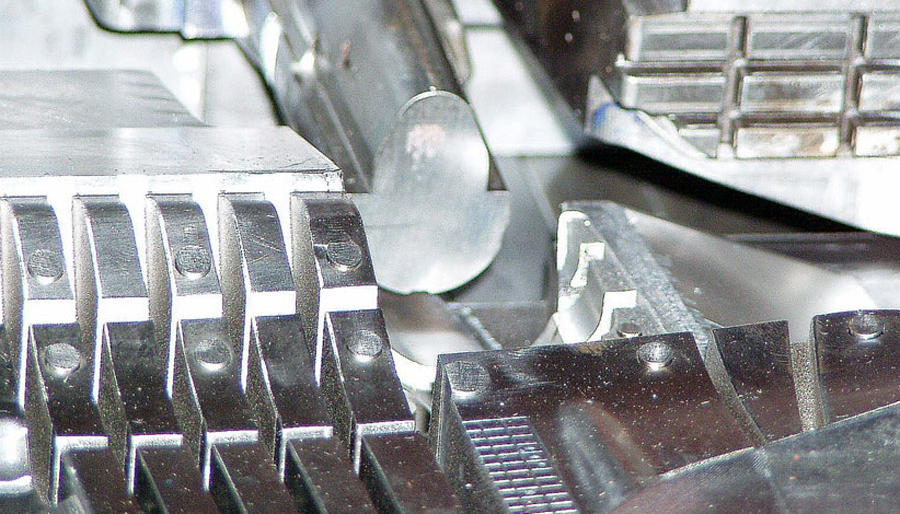
Our business activities for product and process optimization includes:
- Monitoring of projects during the design, manufacturing, installation and commissioning in consideration of target date, technical queries, design changes and elimination of design flaws
- Supplier support in monitoring the manufacturing and inspection process, delivery capacity, installation capabilities of purchased parts, design assistance, project support in production start-ups
- Concept elaboration for new production lines
- Development of new manufacturing technologies for these plants
- Improvement of existing production facilities and process
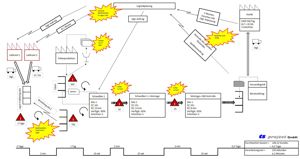
- Identification of waste in the entire process based on the actual situation with the help of a value stream map (VSM)
- Clarification of interfaces between suppliers and customers
- Technical support during the matching
- Creation, acquisition and evaluation of failure and Microstopp analysis
- Implementation of a holistic production system (Total Productive Maintenance (TPM))
- Implementation followed by actions with an Overall Equipment Effectiveness (OEE) analysis
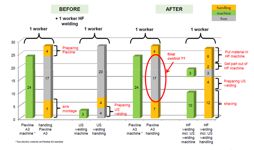
- Time measurements of the production lines including visualization, analysis and optimization
- Identification of improvement potential on the workstations (One piece flow, ergonomics, Poka Yoke, set-up times, CIP, …) and implementation of the identified improvements in the production process
-
Engineering
Creating concepts – Monitoring projects – Technical Documentation
Product Process
Optimization of products and processes in the project
Quality Management
Assistance in failure analysis, new product launches and escalation processes
Fire Protection
Creating emergency and escape plans as well as fire fighting plans
Prototyping
We revise and create 3D CAD data for modeling and procure it for you